What is Lean Manufacturing?
- Laxmi Mathur
- Sep 4, 2024
- 3 min read
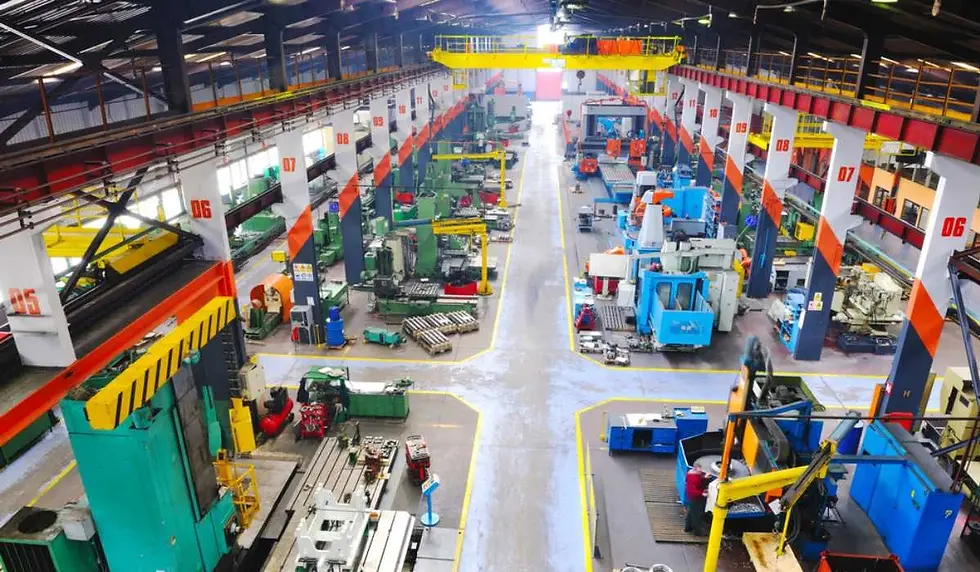
Lean manufacturing is around perhaps of the most exceedingly terrible things that can happen to any endeavor: squandering. Not making the most of every one of your assets is to lose effectiveness and doing so will prompt decreased creation and inability to convey worth to your clients.
The manufacturing industry is, of course, filled with waste. Whether it is idle workers, inefficient production lines or unused materials that cannot be recycled or reused, the results are the same: a loss of productivity. The idea of a lean manufacturing system evolved from the emphasis on eliminating waste and improving the manufacturing process to maximize the value delivered to customers.
Note: Want to get the list of Manufacturing Companies in India? Click on the text link and contact us for all types of companies' databases.
What is Lean Manufacturing?
Lean manufacturing is a production system that focuses on minimizing waste, creating customer value and seeking continuous process improvement. This is achieved by applying lean principles, techniques and tools to eliminate waste from the manufacturing cycle. The lean manufacturing process was first executed in the Toyota Creation Framework (TPS) which reformed the organization's assembling cycle and afterward spread all through the world.
Modernizing your venture the executive's apparatuses can assist your association with expanding efficiency and diminishing squandering. Project Manager, a web-based project the board programming, has all that you really need to smooth out your cycles and further develop creation quality. Create schedules with Gantt charts, execute tasks with task lists, track progress on dashboards and report on everything with built-in reporting features.
Lean Manufacturing Principles
Here are five lean management principles that are applied to optimize lean manufacturing systems:
Identify and create customer value
One of the core principles of the lean manufacturing methodology is to create customer value through the efficient creation of products and services. The first step in the lean manufacturing process is to identify which product features are important to customers and which are not so that you can focus on what is important. Once the customer defines what is valuable, you can create a product that contains only what is necessary and remove the unnecessary work and components associated with it.
Value Stream Mapping
The value stream of a lean manufacturing system can be defined in simple terms as the set of tasks or steps that add value to customers from start to finish during the manufacturing process. The value stream map allows managers to look at each step in the production process to identify waste and improvement opportunities to make the process more efficient and better serve customers.
Create Flow
One of the goals of lean manufacturing is to improve the process. The manufacturing process can be improved by diagnosing waste or inefficiencies such as poorly planned manufacturing facility layout. By fixing functional bottlenecks such as those, you can improve the flow of the value stream.
Pull System
In a pull system, new work is initiated only when there is customer demand. This eliminates unnecessary steps in the production process such as transporting materials, overproduction of products and storing excess inventory, which is considered waste. This is what supports Just-in-Time production.
Continuous Improvement or Kaizen
Kaizen can be translated as continuous improvement. It is a business practice that involves making small, incremental changes over time to a process. In lean manufacturing, kaizen allows businesses to permanently identify problems and develop solutions to maximize customer value and eliminate waste.
It is through these principles that the lean manufacturing system helps businesses improve their production process by eliminating waste. It simplifies the operational structure to understand, perform and manage the work environment. To bring this all together, Toyota implements a mentoring method called senpai and kohai, which means senior and junior. This promotes lean thinking from the grassroots level to the organizational structure.
Comentários